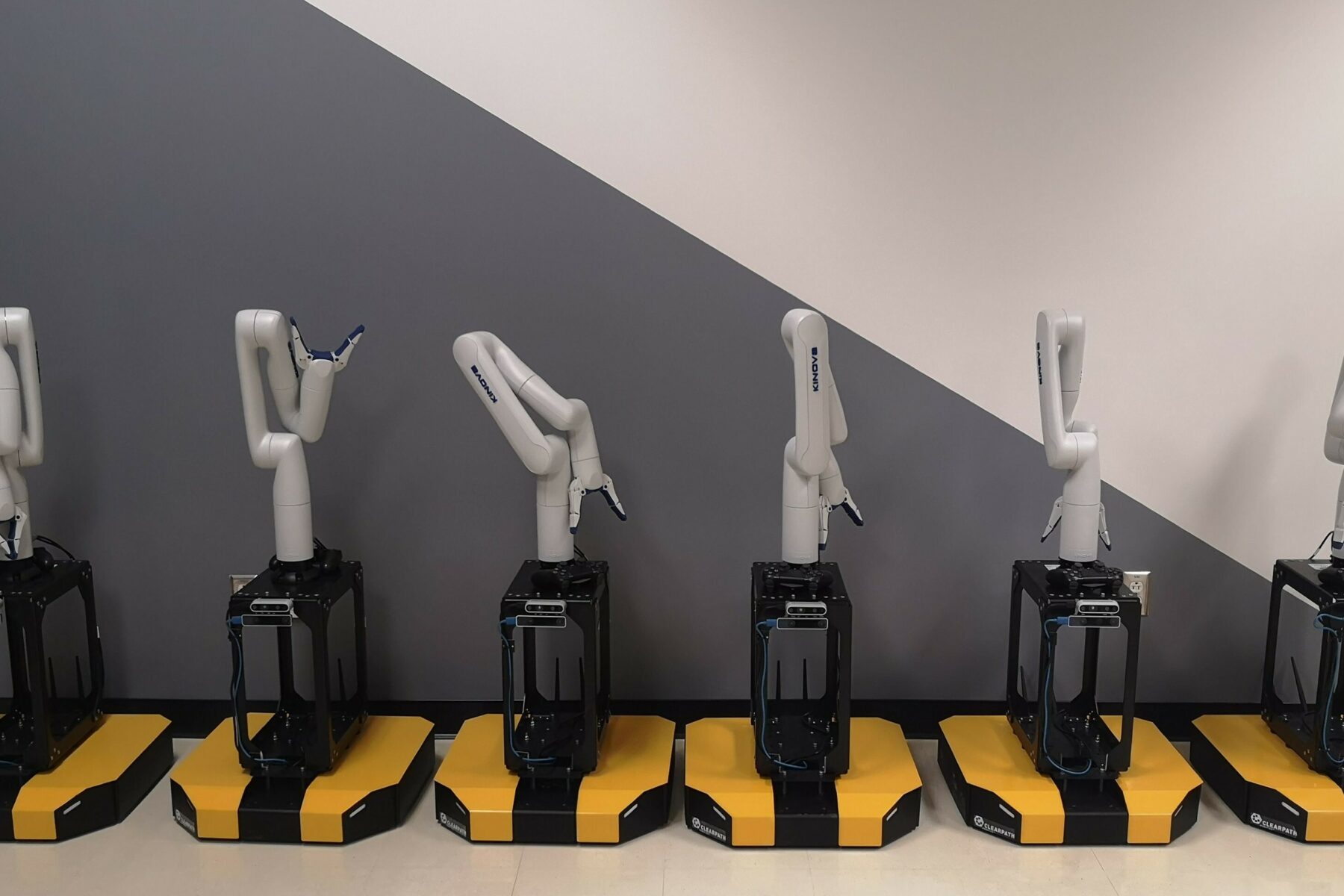
Researches
Enhanced Awareness for Mobile Cobots in Manufacturing Assembly
Year
In progress
Research axis
Human-machine interaction
Among the vast range of robotic architectures available to industry, new paradigms have recently emerged. More specifically, collaborative robotics has experienced an impressive growth in recent years and has penetrated many new markets, especially between SMEs, which were previously reluctant to install robotic and automated devices due to the risk, not only financial but first and foremost with respect to the health and safety of human personnel. Collaborative robots (commonly abbreviated cobots) alleviate this major concern by offering the most attractive feature of being able to work in close proximity with a human being without endangering the latter and not requiring complex and costly safety equipment. Kinova is one of the few Canadian manufacturers of robotic arms, and one of the few worldwide that focus their design on human-centered applications. Still new to the manufacturing sector, their products are already made for the collaborative robotic revolution of the industry. This project aims at developing software, grasping devices and algorithms that Kinova will be providing alongside their products to facilitate their integration in that market. However, we do not stick to the common fixed setup of industrial manipulators, but rather aim at giving Kinova a real edge on the market by focusing on mobile manipulation. Our scenario is several mobile manipulators cooperating to feed manufacturing and assembly stations while maintaining the workers’ safety. For Kinova and for the Canadian robotic industry, it is of the utmost importance to be able to reach and demonstrate high levels of safety. This project will pave the way to testing and validation of mobile cobots deployment in the manufacturing sector. More than validation, this research will address fundamental challenges to the deployment of mobile cobots in the manufacturing sector. Our mechanical engineering approach aims at bringing metrology-level accuracy to the assembly work station even with manipulators on mobile bases. Among our methods we will leverage dual arm dapted grasping device, model-based geometric grasping learning and operator-centric on-table calibration.
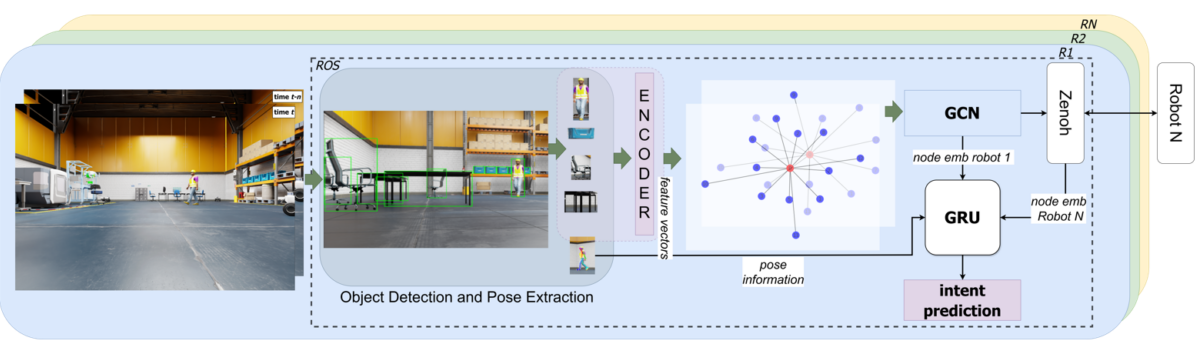
From assistive devices to manufacturing cobot swarms
Ali Imran, Lionel Birglen, Giovanni Beltrame, Bruno Belzile
ReadMinimize tracking occlusion in collaborative pick-and-place tasks: An analytical approach for non-wrist-partitioned manipulators
David St-Onge, Hamed Montazer Zohour, Bruno Belzile
Read